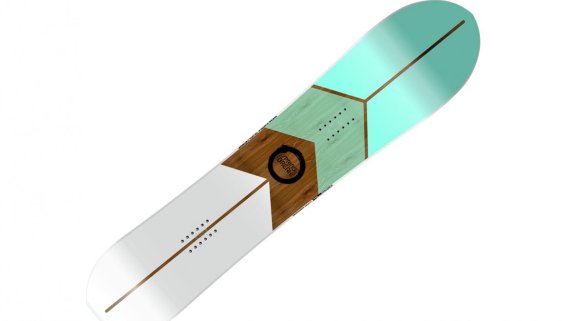
"This could change the construction of snowboards and skis in the long term." Nothing less expects Tom Wilson-North, member of ISPO Award Jury, of the FUS3D Technology from CIME Industries and CAPITA, which was awarded Product of the Year in the Snowsports segment at ISPO Award 2018.
The technology combines 3D printing and winter sports. The wooden core of the board is connected to a tailor-made thermoplastic side panel, which is not only recyclable and therefore particularly sustainable, but also protects the sensitive core and absorbs board vibrations. The result: More powder fun, even more environmentally friendly.
The process developed by CIME Industries is already being applied to the CAPITA boards.
In an interview with ISPO.com, CIME CEO Antoine Postaire talks about the advantages of the new technology, the path from idea to production-ready product and the incredible launch at ISPO Munich.
ISPO.com: How does your FUS3D Technology change the winter sports industry?
Antoine Postaire: At CIME, we have a long experience in ski and snowboard production. We have realized that, on every continent, assembling facilities were facing the same main problem: Supplying the central wood core and the plastic sidewalls for the skis or snowboards production has a very long lead time.
What are the consequences of that?
This is a very important issue because this very long lead time forces the brands to place their orders months before validating quantities with distributors and shops. Those early and most of the time ‘inaccurate’ orders from the brands result in two consequences: Products are either sold out early or in stock.
CIME has worked on a technical process to flexibilize and make the production of the cores and their sidewalls more reactive.
Unfortunately, there was not just one simple moment of genius. At the beginning, there was for sure an amazing idea but it is mostly a lot of work and resilience.
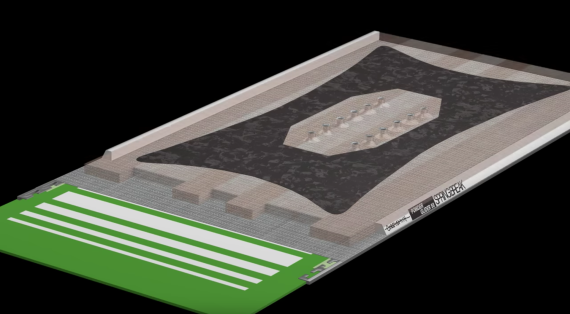
What about the FUS3D Technology has ultimately won the jury over in your opinion?
I think the jury recognized a breakthrough innovation. The FUS3D technology uses a 3D printing technic to incorporate the plastic sidewall to the wood core. When all industries are using mostly 3D printing technics for prototyping, we were capable to turn it into a mass production method.
The FUS3D technology solves the lead time issue mentioned above to offer flexibility and reactivity but it also gives several advantages:
- Costs: Cost effective production
- Quality: Better impact resistance at low temperatures, less return on warranties
- Quantity: No minimum order requirement
- Design: Any sidewall color is possible
- Ecological Aspect: -40% on the consumption of plastic for the sidewall
Where do you still see potential in the winter sports business – especially when it comes to sustainability?
There is still a lot to do in the winter sports industry. Not only when it comes to innovation, but above all when it comes to sustainability. It has to be considered during the very early steps of any company innovation program. This is becoming a need and we are encouraging it with our goal to make the FUS3D technology a new standard in the industry for the production of ski and snowboard cores.
Which feedback did you get on your ISPO Award from the outside?
For CIME, there is for sure a major change now that we are an ISPO Award Product of the Year. There has been three years of ‘secret’ R&D before this award. During this time, nobody was aware of the project, nothing was commented. No positive or negative feedback from the market. ISPO Munich 2018 was the event to launch the FUS3D technology. Launching it with such an award was obviously the best way we could imagine.
How are you incorporating the win into your brand and product communication?
The Product of the Year 2018 label is stuck on every product using a FUS3D core like all the CAPITA Spring Break powder boards for example.
Where is your ISPO Award trophy now?
We are sharing it between CIME INDUSTRIES and our first partner CAPITA MFG. Right now it is at the CAPITA "Mothership", but we are looking forward to displaying it at CIME, where the FUS3D technology has been developed.
- Awards
- Mountain sports
- Bike
- Fitness
- Health
- ISPO Munich
- Running
- Brands
- Sustainability
- Olympia
- OutDoor
- Promotion
- Sports Business
- Textrends
- Triathlon
- Water sports
- Winter sports
- eSports
- SportsTech
- OutDoor by ISPO
- Heroes
- Transformation
- Sport Fashion
- Urban Culture
- Challenges of a CEO
- Trade fairs
- Sports
- Find the Balance
- Product reviews
- Newsletter Exclusive Area
- Magazine