- Understanding the Importance of Water as a Precious Resource
- Implementing Dye-House Rules
- Opting for Dope-Dyed Yarns
- Recycle Textile Waste – From Trash to Treasure (T-2-T)
- Exploring Water-Reducing Structural Solutions
- Leveraging Advanced Printing Technologies
- Considering Lab-Grown Cotton
- Promoting Water-Saving in Domestic Laundering
- Innovating in Footwear Manufacturing
The textile industry has always had a high water consumption – with textile production requiring water for a variety of stages from preparation, sizing, desizing, scouring, bleaching, dyeing and printing. An estimated 93 billion cubic meters of water used, including cotton farming, annually according to Ellen MacArthur Foundation: A new textiles economy: Redesigning fashion’s future, but, as a more responsible and accountable industry emerges, the use of water is being reduced in a variety of ways.
Responsible textile mills also invest in the latest efficient dyeing machinery, signed to reduce the use of water. But there is a host of alternative developments happening, that are less reliant on traditional dyeing methods, leading to mass reduction in our water use, as well as cost savings.
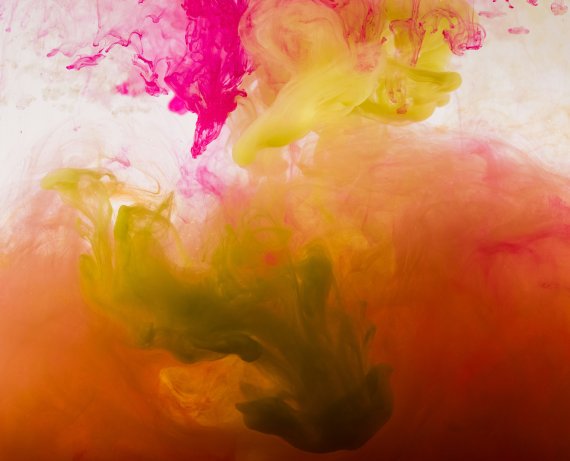
Recycling water and waste water treatment plants are the norm now in the textile mills that maintain strong sustainable values and a high regard to efficient manufacturing and use of resources.
Key among these is low liquor ratio dyeing equipment that significantly reduces water consumption and energy-efficient, on-demand boilers that substantially reduce dye house emissions and the latest dyeing equipment that has a superior level of efficiency and reduced waste.
Looking to awarded companies at ISPO Textrends, it is clear to see the importance water savings have. Toread has developed and implemented a new approach to textile production. They introduced low-carbon dyeing technology, saving water and energy. CO2 dyeing involves using supercritical carbon dioxide, a state of carbon dioxide where it exists as both a liquid and a gas, as the dyeing medium. This innovative approach minimizes the water consumption and reduces the environmental impact associated with conventional dyeing methods.
Synthetic dyes, have long superseded original dyes, with dye stuff providers developing cleaner chemical solutions for today’s colorways. Today natural dyes are making a return, predominantly with cellulosic fabrics, however Noyon Lanka, a subsidiary of MAS Holding, has launched Planetones, is the world’s first 100% natural dye solution, applicable to nylon, as well as cotton and wool materials.
A test comparison was carried out between Planetones and the traditional synthetic dye process, resulting with a water saving of 43 - 62% and electricity saving of 62-70% respectively.
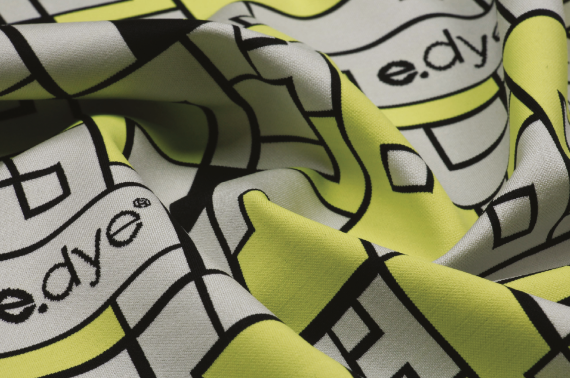
For synthetics dope dyed/solution dyeing is a water-saving solution. In the context of textile industry water consumption, this method significantly reduces the need for water-intense dyeing provesses. For dope dyed yarns, in bio, recycled and conventional polyester, nylon and spandex, the color batch is applied at the extrusion of the yarn. The benefits of this is that you get an even surface with barely no rejected fabric, as an even colorway is achieved. With the exclusion of traditional dyeing process, the water saving is significant.
ECLO is an innovative dope yarn technology awarded by ISPO Textrends, offering a high level sustainable polyester fabric for outdoor and fashion industry with excellent colorfastness.
Combined with the newest AIRSHIFT nano-membrane, the fabric releases double times breathability and storm waterproofness as well as great air permeability. The fabric is perfect for outdoor garments.
Leading polyester yarn supplier, e.dye, offers their Waterless Color System Technology for polyester. Requiring 85% less water, 90% less chemicals and 12% less CO2 emissions compared to traditional piece dyeing, this innovation plays a crucial role in addressing textile industry water consumption concerns. The range of colors available is appealing, with high color fastness and no migration, allowing contrast color-blocking in jacquards and instarsia structures without risk.
FENC has incorporated solution dyeing processes for its carbon capture polyester. The world’s first waste gas reuse technology, cooperation with Lanza Tech captures CO2 released from steel factories, converting the waste gas into ethylene glycol and polymerizing it into polyester. Accomplishing CO2 negative and reducing GHG emissions by 24% by combining Solution Dye Tech to skip the dyeing process, the products save 61% water, energy consumption is reduced by 67% and reduce GHG emissions by 85%. By incorporating the solution dye process, fabrics result in better sunlight protection, less discoloration and improved washing fastness than the traditional water dyeing process
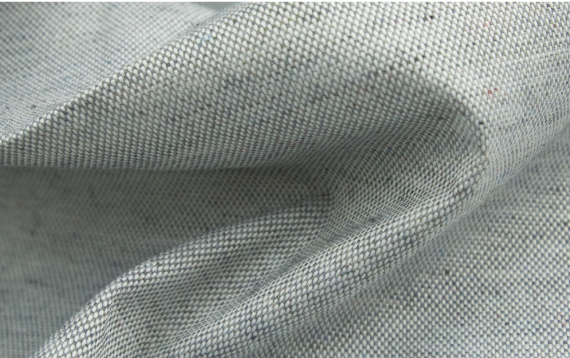
With circularity at the forefront of the textile industry, companies are looking to return waste into the circular economy. One of the most obvious is fiber and textile clippings that have in the past been discarded. By eliminating the traditional dye process, these waste materials – already dyed – are collected shredded, and spun into arn, significantly reducing textile industry water consumption.
Aclima, the Norwegian wool specialist brand, launched ReBorn, a range of knitwear manufactured from fabric cuttings from their factory floor. Similarly, LMA has incorporated yarn waste, giving trash a second life. The combination of recycled cotton and recycled polyester brings forward a special texture, resulting from the combination of all the different fibers.
Focused on the concept of no dyeing, the knit has appeal, a great hand feel but uses significantly less water, less energy, less CO2 emission and no chemicals. But, perhaps more importantly zero waste,
‘I’m Trash’ is the name Honmyue gave to their development to highlight the need to use the already dyed waste. An attractive and sustainable recycled material, ‘I’mTrash' provides an eco-luxury look and speckled effect by blended fibers.
Fibers are processed from colorful discarded garment waste and retain the original fabric color. It requires no dyeing and therefore reduces water waste, carbon emission and energy use. The fabric is made from pre-consumer PET fiber waste and post-consumer recycled Polyester. 100% recycled material is in the process of being GRS certified. Compared to virgin Polyester, it saves energy, reduces carbon emissions and prolongs landfill life.
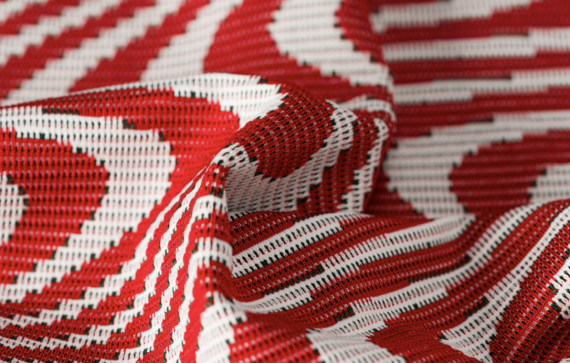
Yarn printing and dyeing is also becoming a popular option, eliminating the more water heavy process of piece dyeing. By working with already colored yarns, specifically in jacquard structures, innovative surface effects can be created.
An interwoven 3D Jacquard from Lee Ven incorporates yarn-dyed technology, utilizing recycled polyester but also reducing water consumption.
Wujiang Tutaike is also using recycled polyester yarn in both warp and weft side. That isn’t just the eco aspect, alongside removing plastic from the environment, by manufacturing an IKAT construction combined with large jacquard process, the printing process, already applied to the yarn, is highlighted after weaving, presenting a rise level of blurred graphics, eliminating the margin for error as compared to printing.
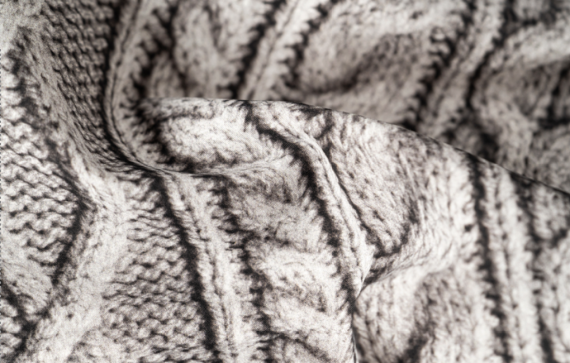
Technology contributes to drive the textile sector at all levels, from spinning through to finishing. New digital printing technology is becoming a new option for prints.
One company has gone the extra mile, developed and implemented a new approach to textile production – the world’s most advanced coloration technology, to be exact. NTX Cooltrans has the lowest environmental impact, doesn’t affect the handful of the substrate fabric and also offers companies more control in the finishing and coloring of textiles.
This innovative process colorizes a variety of substrates — natural, man-made, or synthetic, without the need for water or heat. The result is a remarkable reduction in textile industry water consumption, making it a game-changer for sustainability in textile production.
The combination of precision engineering, advanced dye chemistry, and machine learning results in rich, deep and brilliant colors that fully penetrate the substrates without compromising hand feel, engineered structure, or the bottom line. The definition that NTX Cooltrans offers is outstanding, and the benefits to textile suppliers and garment manufacturers are key. With this technology, there are no minimums, leaving textile manufacturers to colorize only the greige fabric they need, rather than having excess rolls of dyed or printed fabric as deadstock, leading to a higher level of creativity and control.
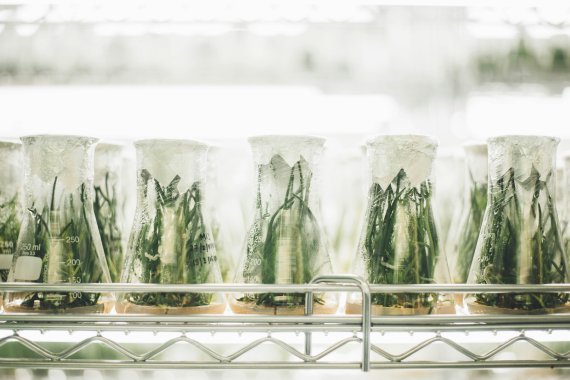
When accounting for the approximate amount of water the textile industry uses, 93 billion cubic meters of water annually, this also include cotton farmers. The reason being that cotton is a water intensive right from the seed, this is why it is with some interest that Galy, a US-based start-up, has amassed some big names from the textile sector, investing in cellular agriculture, the first being Literally Cotton.
To create Literally Cotton, Galy places cells from cotton plants in bioreactor tanks, and by precisely controlling the conditions inside the bioreactor, Galy coaxes the cells into growing into cotton fibers that can then be harvested, dried, and used like any other cotton. The water needed to grow cotton is eliminated as is the use of pesticides.
Established in 2019, Galys has long way to go, against a cotton industry that has been established for thousands of years, but it certainly has an interesting outlook, especially taking into consideration climate change and global droughts that blight the cotton industry.
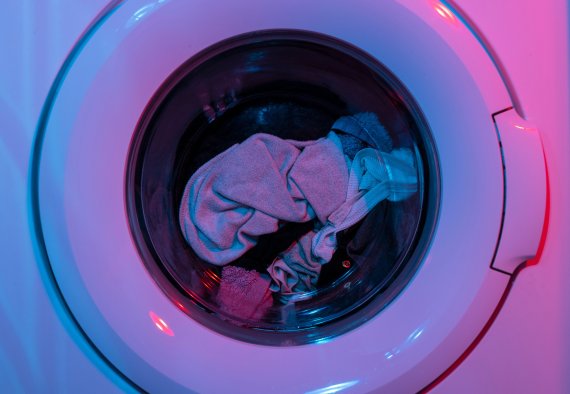
Whilst the textile industry gets the brunt of the water backlash, it is in fact the home launderings of a product that uses the most water and impacts the environment.
Polygiene, a pioneer in odor control solutions, was one of the first companies to put the spotlight on domestic launderings through the publication of an Life Cycle Assessment (LCA). Their findings highlighted that washing half as much reduces environmental impact by on a third. Less washing also extends the life of a garment and saves the consumer time.
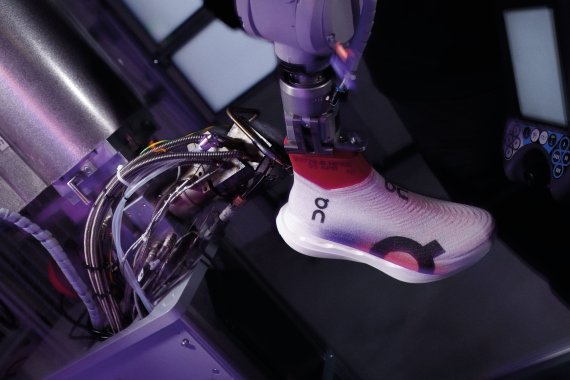
To finish off on our water saving sojourn, we have to include ON’s new Lightspray show. Launched just in time for the Olympics, ON has united robotics and materials innovation, to create a spray upper performance shoe.
The unique manufacturing process cuts a decades-old, multi-part process into a three-minute, minimal-waste step – including reducing CO2 emissions by 75% and significantly decreasing textile industry water consumption that would have previously been used in traditional textile manufacturing. As we say, every drop counts!
- ISPO TextrendsThese are the winners of ISPO Textrends Spring/Summer 2027
- ISPO awards
- Mountain sports
- Bike
- Fitness
- Health
- ISPO Munich
- Running
- Brands
- Sustainability
- Olympia
- OutDoor
- Promotion
- Sports Business
- ISPO Textrends
- Triathlon
- Water sports
- Winter sports
- eSports
- SportsTech
- OutDoor by ISPO
- Heroes
- Transformation
- Sport Fashion
- Urban Culture
- Challenges of a CEO
- Trade fairs
- Sports
- Find the Balance
- Product reviews
- Newsletter Exclusive Area
- Magazine