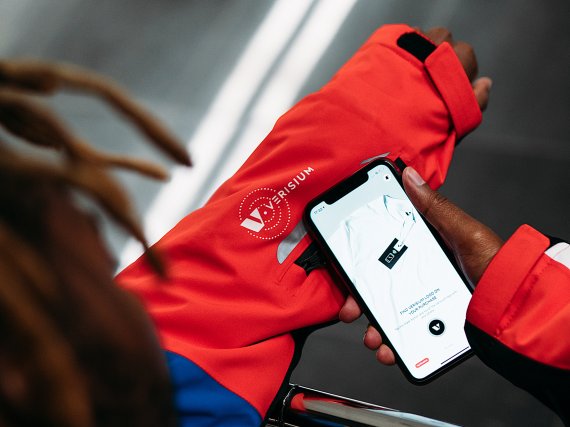
How does a cyclist protect himself from environmental influences such as rain and wind? Waterproof and breathable membrane fabrics are essential components of both outdoor and urban functional clothing.
The decisive factor here is to find the right balance between the two characteristics for the respective use and situation. Does The North Face achieve this balance with the new Futurelight membrane?
Using nanospinning technology, a variant of electrospinning, The North Face produces very thin polyurethane fibers. The polymer solution is accelerated away from an electrode by means of an electric field, so that the smallest fibers attach themselves to the counter electrode like a fleece.
The size of the resulting pores is only in the nanometer range, which makes the membrane permeable to air and water vapour at the same time, but impermeable to liquid water. By varying the viscosity, surface tension and charge density of the liquid, the breathability, elasticity and structure of the membrane can be adapted to the intended use. For example, the material can be optimized for competitive sweat sports or protection in wet and cold climates.
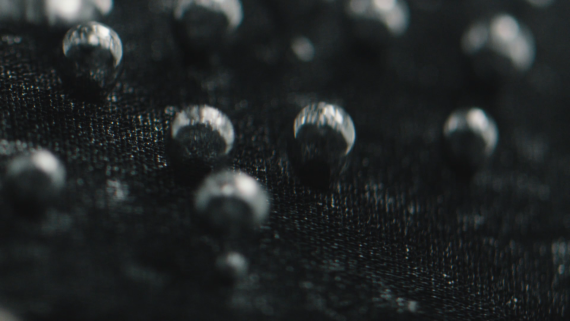
The Futurelight membrane is supported by lamination with nylon and polyester layers that protect against abrasion and can be manufactured from recycled raw materials. The water-repellent coating, which helps maintain breathability in the rain, consists of PFC-free hydrocarbons and is incorporated directly into the fiber, allowing it to retain its functionality for up to 80 washes - longer than conventional coatings.
Futurelight-based garments have been available since October 2019. Further information can be found here.
Can membrane jackets protect against injuries in the event of a fall from a bicycle? The ingredient brand GRDXKN (pronounced: grid-skin) wants to make this possible soon.
In 4D printing processes, materials are 3D-printed that can be changed over time or environmental influences. In the GRDXKN process, cross-linked polygons of dyed polyurethane are printed on textiles, which are thermoformed during the printing process and form a three-dimensional structure.
Originally used as a purely aesthetic addition, certain structures are followed by functionality. For example, structures on the inside of the textile can prevent skin abrasion in the event of a fall from the wheel. At the same time, GRDXKN is researching the improvement of the aerodynamics of clothing through 4D pressure structures.
The process is currently being patented and is still being researched. In principle, printing from 0.5 to 4 millimeters thick is possible on all hydrophilic materials, such as cellulose fibers or polyester. Water-repellent finishes must be applied to the fibres after printing.
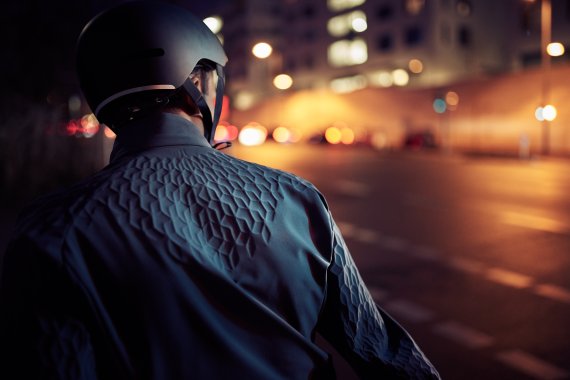
The possibilities range from adjustment to the personal requirements of individual carriers (individual prints) to variable strength/flexibility of the print by adjusting the print material and print pattern. Further information about GRDXKN can be found here.
How do manufacturers and sellers best inform their customers about product features? The Moscow start-up Verisium offers an exciting opportunity.
NFC chips were originally intended to be incorporated into clothing to make illegal imitations of branded goods more difficult, but Verisium has found new applications for them. The Near-Field Communication Protocol enables devices such as smartphones to interact with the chip.
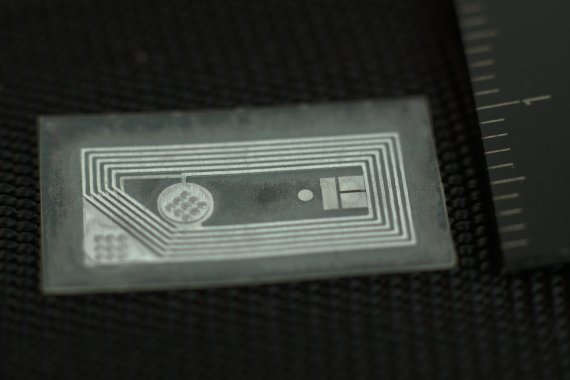
After scanning the chip, users receive information from the clothing manufacturer, such as links to further websites, video and audio files. This enables direct customer interaction, which can be used creatively for marketing purposes.
Buyers of Cloudburst Wear products received personalized invitations to Paris Fashion Week 2019 when they scanned the garments. Additional information on products (location of secret pockets) or other possibilities can also be used to express the individual story of the brand.
In addition, data such as the frequency of scans or the location of scanning processes can be collected and evaluated. In case of multiple scans of the same product a special price can be offered. Further information about Verisium can be found here.
Electronic components in functional textiles can not only improve customer interactions, but also save human lives. But how? Many wearables are currently available that record vital functions - heartbeat, body temperature, GPS signal (Movesense sensors). There are also satellite systems that enable rescue operations from emergency situations in remote areas (ProteGear).
The next step in the development of such technologies is the implementation of the functionalities directly into the textile product. Smart textiles are equipped with at least one sensor and one computing unit (microcontroller), sometimes also actuators that can react actively to environmental influences.
Here, too, there are already products that regulate the performance of a heating system integrated into clothing, for example, depending on the body temperature and ambient temperature.
The durability and washability of textiles remains a previously unsolved challenge: Either they cannot be washed at all with normal washing cycles, or the functionality of the electronic components is only guaranteed for a limited number of washing cycles. At the Institute for Textile Technology (ITA) of the RWTH Aachen, research is being carried out to improve these properties.
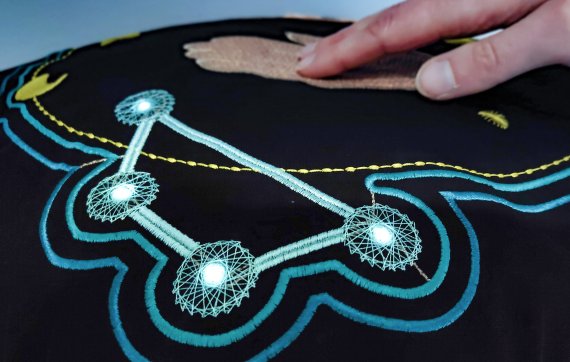
Smart textiles are particularly needed in sports, medical and military applications. For example, moss embroidered electrodes can be incorporated into functional jersey sports shirts.
These send information such as an electrocardiogram (ECG) to a microcontroller via conductive tracks made of embroidered, conductive yarn, which processes and displays the information. Piezoelectric (pressure sensitive) sensors can also be used in garments to represent touch controls for necessary electronic devices.
ITA is also working with partners in Germany and Korea to develop processes that enable complex Smart Textiles to be mass-produced. More information about the ITA of RWTH Aachen University can be found here.
- ISPO TextrendsMore diversity outdoors: Polartec leads the way