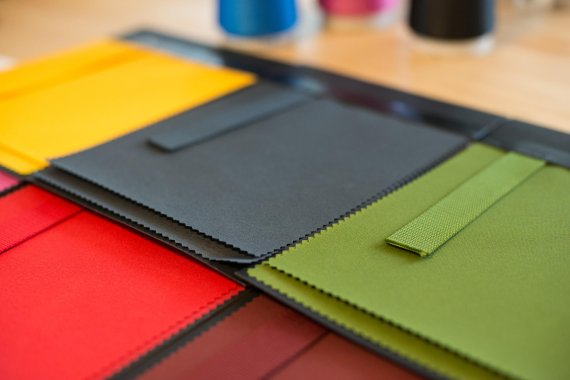
Little water consumption, sustainable, colorfast and without fading: The company We are SpinDye has developed a method that could revolutionize the production of synthetic fibers and thus of pants, jackets or backpacks.
The Swedish company dyes synthetic fibers - and does so completely differently than all other textile companies have done so far: sustainability and environmental protection are the focus. Above all, the immense water consumption is significantly reduced by the innovative process.
The idea behind We are SpinDye is actually quite simple: First, recycled plastic is melted, then the desired color pigments are added to the undyed material. This is then used to produce yarn in the desired thickness. The customers and manufacturers can then process this yarn as usual.
We are SpinDye: conserving resources
"Our company is built on the principle of least harm to the environment," says CEO Martin Berling: "We use hardly any water, produce virtually no waste, and the use of chemicals is also kept to a minimum."
This is in striking contrast to the conventional dyeing process: 100 to 150 liters of water are needed to dye a kilogram of textiles. Due to a lack of regulations in countries such as China or Bangladesh, the toxic water ends up in rivers, lakes and groundwater after dyeing. According to Greenpeace, two-thirds of all rivers and lakes in China are already classified as polluted.
Dyeing technology does not need large machines
We are SpinDye offers its technology for all synthetic materials such as polyester or nylon but also for viscose. A combination of synthetic fiber and unbleached cotton can also be used. In further processing, there are no limits for the manufacturers: The fabrics can be coated or provided with a membrane, for example.
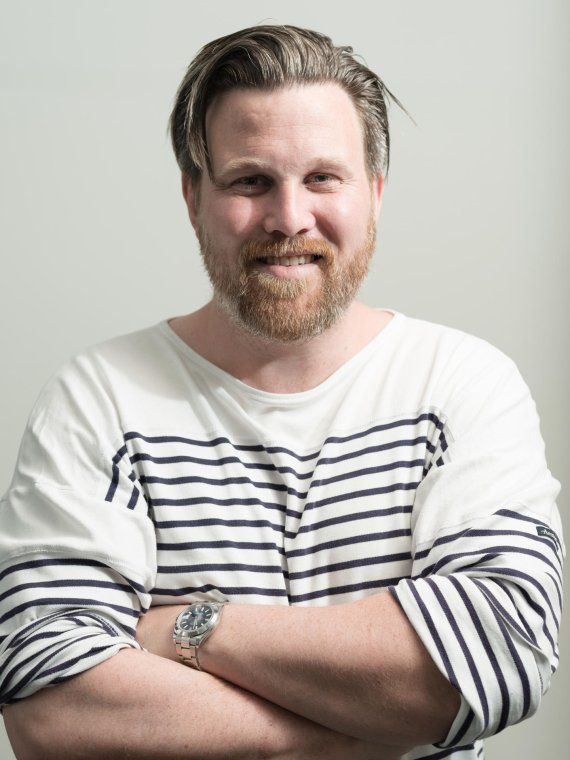
Of course, We are SpinDye from Sweden is not the only company that has developed a water-free dyeing technology. Nike and Adidas, for example, also have processes with ColorDry or DryDye that do not require water for the dyeing process - and have done so for several years.
However, CEO Berling does not accept this argument: "In contrast to these technologies, we don't need large machines for our process because we already add the color during the production of the yarn."
"Sports industry has greater environmental commitment"
On the other hand, another aspect is almost more important to Berling: "We want to digitize dyeing!"
What he means by this is that in the future, manufacturers will be able to select the final product color on a digital color scale. Since the synthetic fibers are already dyed during their manufacture, color authenticity is guaranteed. The tedious process of color matching is eliminated. In addition, color fastness is maintained even under extreme UV irradiation. The company currently offers around 2000 colors.
At ISPO MUNICH 2017, the Swedes want to present themselves to a large professional audience for the first time. "ISPO is simply the trade show. Of course there are other textile fairs," says COO Andreas Andrén, "but we think the sports and outdoor industries have a greater environmental commitment and are more interested in technical innovations."
There are many driving forces at ISPO MUNICH, says Andrén: "Even though we are not a sports or outdoor brand per se, we want to start here!"
- Awards
- Mountain sports
- Bike
- Fitness
- Health
- ISPO Munich
- Running
- Brands
- Sustainability
- Olympia
- OutDoor
- Promotion
- Sports Business
- Textrends
- Triathlon
- Water sports
- Winter sports
- eSports
- SportsTech
- OutDoor by ISPO
- Heroes
- Transformation
- Sport Fashion
- Urban Culture
- Challenges of a CEO
- Trade fairs
- Sports
- Find the Balance
- Product reviews
- Newsletter Exclusive Area
- Magazine